Installation
Limestone, sandstone and all natural stones are products of nature and no two pieces are exactly alike. Stone may vary in colour, tone and have lines of quartz, fossilisation and other markings. There will also be small variations in all dimensions. The tiles will arrive in much the same order as they came off the saw, which means that shades of colour and particular markings in the stone are liable to be next to each other. You should look at the material to establish its colour and marking characteristics, and should ‘shuffle’ the pieces from different batches before fixing to create a random pattern. Mixing the tiles up will spread these variations naturally over the floor. Any other design details should be agreed before installation.
Stone can be fixed to a suspended floor (with marine plywood or a combination of marine ply and tile backer board) or to a solid concrete sub-floor. Flexible additives to the adhesive and grout are necessary to take up any movement if the stone is being fixed to a suspended wooden floor or over under-floor heating.
The stone is vulnerable until it is fixed, and still vulnerable until it is treated against staining. It may arrive on site wet. This does not prevent it being fixed but it cannot be treated until it is dry.
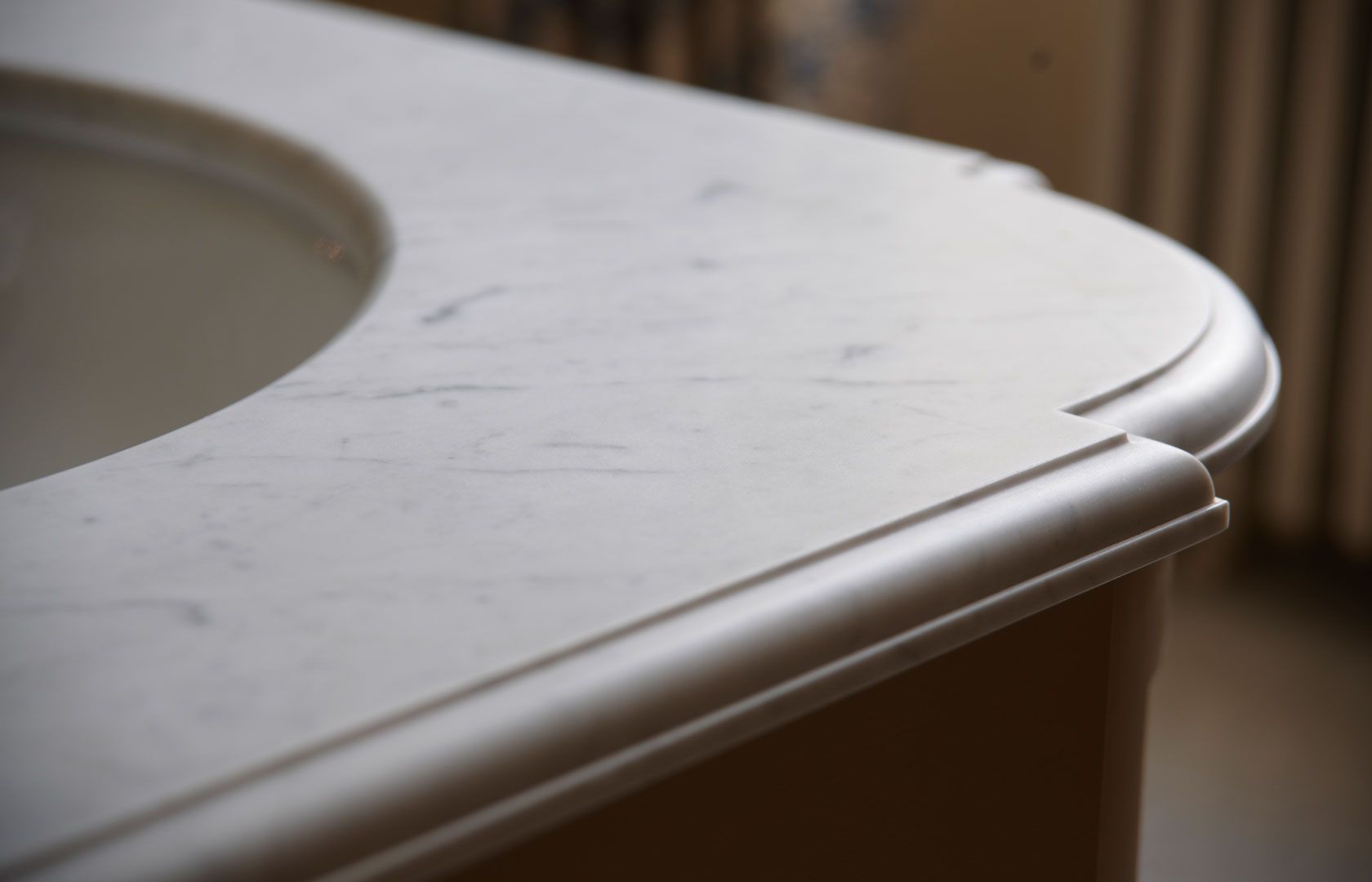
- Unpack all the tiles before starting work. You should mix the batches of stone, to even out any variation.
- Wash all the tiles as they may have left the producer wet, and may include a residue from any finishing process.
- Allow the tiles to dry completely before installation. This will allow you to identify any funny or tonal markings that you do not want to dominate, and use these tiles in less visible areas or for cut tiles.
- If you need to install your tiles quickly, or want to leave the installation of the floor until all other trades have completed, then consider using our pre-dried and pre-treated tiles.
- Do not be surprised to see some minor damage to some of the tiles, incurred during packing or unpacking. These should be used for cut tiles.
- If you are using tiles of different thicknesses – for example riven slate – grade the tiles before installation. The thickest tiles will dictate the floor level. You should install these first and bring the others up to the same level by bedding them with an appropriate adhesive.
- Be aware that there will be some slight natural variation in dimension and thickness with all your stones, because you are working with a natural material.
- Ensure that all areas to be tiled are flat, level, clean and dry before starting installation.
- Discuss your detailed requirements with your stone fixer before they start work.
There are several different ways of fixing flooring. Whether you fix to a normal screed, an anhydrite screed or with an adhesive, we recommend a gap between tiles of between 2 to 3mm depending on personal preference. We do not recommend that the tiles be butted up, as the size of the tiles will inevitably vary slightly.
The edges of the tiles will not have been calibrated and are only sawn - a good fixer will “kill” the edges by rubbing each tile with a diamond pad as it is fixed. This removes the very slight chipping of the edges that was caused by the saw.
Fixing into a screed
- Make sure that the sub-floor is firm, clean and dry. You should have a screed that is at least 35mm deep for 20mm stone. The mix should be 3 parts washed, sharp sand to 1 part white cement, used semi-dry.
- Butter the back of the stone with an adhesive slurry before fixing the stone in the screed. To prevent the stone drying out too quickly, which may result in some tiles not sticking properly, either wet the stone before fixing or paint the back of the stone with a bonding agent.
- If you are fixing a light-coloured stone, use a white cement-based adhesive.
Calcium Sulphate or Anhydrite Screeds
- Make sure that the screed has cured thoroughly in line with the manufacturer’s recommendation before starting tiling. This is essential as these screeds retain moisture for much longer than a conventional sand and cement screed.
- Do not start tiling until the screed has a residual moisture content of less than 0.5%.
- If it is necessary to start tiling earlier, ensure that the floor is completely dry, and use a decoupling membrane such as Schlüter-DITRA, otherwise moisture will be trapped beneath. DITRA must be used, as a cement-based adhesive will not bond and hydrate the screed.
- Remove any fine laitance on the surface of the screed, and abrade the surface to help the adhesive key in.
- Seal the surface of the screed before fixing the tiles.
Using an Adhesive
- You can fix the stone to a concrete screed or to a suspended plywood sub-floor. But you must ensure that the floor is as rigid as possible.
- Please check the following with your builder and/or tiler: a flexibility additive should be used in the adhesive and grout, especially if you have a suspended floor or have floors with underfloor heating.
- Before fixing the tiles, ensure that the sub-floor is true and level, free from contamination and loose areas and properly prepared to give a good bond. Ensure that the background to be adhered to is thoroughly dry, solidly bedded, and free from dust and friable matter. Some fixers will paint the sub-floor with a bonding agent.
- Make sure the back of the stone is free of dust and other contaminants. Fix tiles with adhesive in accordance with the recommendations of the adhesive manufacturer.
- Stone tiles, especially in larger sizes, can vary in thickness, so it may be necessary to build up the adhesive to ensure a floor with a minimum of “lipping”. Always start with one of the thicker tiles.
- Press tiles onto the adhesive and tap firmly into position. It is essential to lay each tile on a solid bed of adhesive with no voids. If any adhesive gets on the face of the tiles, clean it off immediately.
- To fix stone to metal supports, bond with a grab adhesive such as PL200.
- Use a white cement, as coloured cement may seep through to the face of the stone. Paint the back of the stone with a bonding agent to inhibit any leaching.
- We always recommend using Ditra Matting or Ditra Heat
Grouting
- Test a small area of the floor to make sure the grout colour and texture is suitable. Grouts come in many colours - we recommend using pale neutral colours to matching the palest element in the stone. Cement, sand and silver sand can also be mixed in various proportions to suit the stone.
- Most fixers prefer to apply one coat of impregnator or sealer to the stone before grouting, which acts as a grout release. (Make sure the stone is clean and dry before application of the protection and allow it 24hrs to cure.)
- Grout the joints so that they are completely filled. The grout should be very liquid and pushed in firmly so it goes right into the gaps. We recommend that the face of the stone be completely covered with grout to avoid any possibility of ‘picture-framing’.
- Open-faced stones should also be grouted across the face of the tiles in order to fill up any larger holes.
- As the work proceeds, thoroughly clean the grout off the surface using damp cloths or sponges. Tool the joints smooth.
- Stone for exterior use should normally be a minimum of 30mm thick.
- It is important to minimise moisture retention in the stone. Exterior paving (including Treads) should be fixed to a “fall” to allow water to run off. Cross falls should be 1:40/60 & longitudinal falls should be 1:80/100.
- Protect the stone from water in every possible way. Ingress of water from anywhere other than the surface (particularly via the Sub-structure) will probably cause damage to the stone. The preparation work is CRITICAL.
- Exposed edges or voids within the adhesive can allow water to be sucked into the unseen faces of the stone and could cause frost-damage in hard winters.
- If you are using expansion joints for the sub-structure (discuss with an expert if this is needed) then the line of the stone should line up with the expansion joints.
- The unfinished edges of the stonework around a patio or terrace should be solidly infilled and finished and there should be a “Mowing Strip” or an edging detail (www.everedge.co.uk ) between the stone and soil or turf – particularly if you are using white stone. The purpose of this is to minimise any contact between the stone and moisture-retaining elements such as soil or turf.
There are a number of ways to fix the stone.
Fixing to a screed
- Make the foundation (eg. MOT ‘Type 1’) firm (typically it should be ‘whacked’ seven times!), and should be clean and dry. We recommend a MOT depth of 4 inches and a screed depth of at least 50mm. The mix should consists of 4 parts of washed sharp sand to 1 part of white cement, plus a flexible adhesive or plasticiser which will act as an anti-frost element. Make the mix a little wetter than usual to ensure you get a solid bed.
- Drag the screed across the area to create a solid bed with no voids, which is 5-8mm higher than the desired finished level. This will allow for compaction of the bed when you tap the stone down.
- Before laying the stone, make sure the back of the stone is clean. It is a good idea to apply a PVA bonding agent to the back of the stone - (Steintec make a good range of mortars, including a bonding agent for the back of the stone).
- Butter the back of the stone with an adhesive slurry (cement may dry too quickly) before fixing the stone in the screed. Tap the stone down firmly to ensure solid bedding.
Fixing with adhesive to a new concrete screed
- Ensure that the base is true and level, and free from contamination and loose areas.
- Fix tiles with adhesive (including a flexible additive that will works as a frost-resistant additive for exterior use) in accordance with the recommendations of the adhesive manufacturer.
- Apply a PVA bonding agent to the back of the stone.
- Butter the back of the stone with adhesive slurry.
- Press the tiles onto the adhesive and tap firmly into position. If any adhesive gets on the face of the tiles, clean it off immediately.
Loose laying or placing on Buzon Pods (or similar) adjustable supports
- Make sure that the support is appropriate to the weight and thickness of the stone - take advice on this from the support manufacturer. Remember that thinner stone will need closer supports – typically at centres of 10-20cms.
- Stone thicknesses can vary by +/-2mm so you will need to use adjustable supports that can accommodate these tolerances. You may need to use rubber softening strips between stone and support to allow some “give” and to help prevent damage resulting, for example, from a piece of grit acting as a fulcrum between the stone and the hard plastic of the support.
Grouting
- If you are mixing your own grout, make sure that it suits the stone colour, and use a flexible additive for frost resistance. Test a small area to make sure the grout will look right when it is dry.
- It is becoming increasingly common to use a ready mixed product. A good range is available from Stonefix.
- Gaps between tiles may be between 3 and 10 mm depending on personal preference.
- If you are using a “slurry grout” system, apply one coat of impregnator to the stone before grouting, to help in washing the grout off textured surfaces. The stone must be clean and ideally should be dry (use a water-based impregnator if the weather prevents the stone drying) before the application of the protection. Make sure you allow enough time for the impregnator to cure, before applying the slurry grout.
- Grout the joints so that they are completely filled. The grout should be pushed in firmly so it goes right into the gaps. Pull the grout across the face to fill any voids and to avoid ‘picture framing’.
- As the work proceeds, clean the surface thoroughly with a sponge. Tool the joints smooth.
Pointing
- You can use a dry mix of cement, sand and silver sand instead of grout. This will allow moss to grow between the tiles.
- Mix the materials in proportions to suit the stone colour.
- All good quality limestones or marbles will perform well as floor and wall tiles, provided they are properly protected with a resin-based, penetrative sealant or are flood-treated with a silicon-based impregnator.
- With proper treatment many limestones and marbles can also be used successfully as vanity tops and bath surrounds.
- The tiles themselves will not provide a waterproof layer. Thorough waterproofing must therefore take place behind or beneath the tiles to prevent water getting into the walls or the floor structure. This process is known as ‘tanking’. We recommend the use of Schlüter-DITRA waterproofing membranes.
- Stone for use in areas that regularly get wet (ie showers or baths) should be ‘flood-treated’ with at least three applications of Lithofin MN Stainstop before use. This should prevent water soaking into the stone but will still allow it to breathe.
- Where appropriate, the stone should be fixed to ‘falls’ (that is with a small slope leading to a drain) to minimize the risk of standing water which would eventually soak into the stone - any standing water that there is should be wiped away.
Limestone and marble will create beautiful worktops and we will supply them as fully protected as possible. However, it is impossible to prevent some marking, particularly when the worktop is new. As the stone ages, it will become more difficult to mark as oils will penetrate the stone and provide further protection, and the marks that have been made will fade. If you look after it properly, you will end up with a durable and handsome worktop. But if you are looking for a ‘perfect’ finish, then you should probably consider other materials.
In order to minimise marking wipe off any spills as soon as possible. Highly coloured foods such as curries will leave the most obvious stains, particularly on light-coloured stones. Dark coloured stones are particularly susceptible to ‘water’ marks (which in fact usually come from alcohol).
Choose adhesives and grouts that are both appropriate to the performance needed and will match your stone in colour. When using adhesives and grouts, always follow the manufacturer’s recommendations both in terms of using their products and also with regard to which other products are compatible or incompatible.
Good ranges are available from Stonefix and Ardex.
A decoupling membrane allows the stone to move independently of its substrate which will help guard against cracking of the stone. We recommend decoupling membranes Schluter such as DITRA